For the first time in history, the use of green hydrogen as a primary energy source is nearing reality. Whether in large-scale power generation, heat provision, transportation fuel or industrial applications, the potential of this clean gas is enormous. Goldman Sachs predicts that by 2050, green hydrogen could supply up to 25% of the world's energy needs, becoming a total addressable market worth US$10 trillion . PWC expects that by this same date, the gas could displace around 10.4 billion barrels of oil equivalent—around 37% of pre-pandemic global oil production—and could lead to the creation of some 400,000 jobs globally across the hydrogen supply chain . Within the same time frame, the Hydrogen Council believes adopting green hydrogen could reduce annual carbon dioxide (CO2) emissions by 18% based on present-day volumes—a significant contribution to realising a net-zero world.
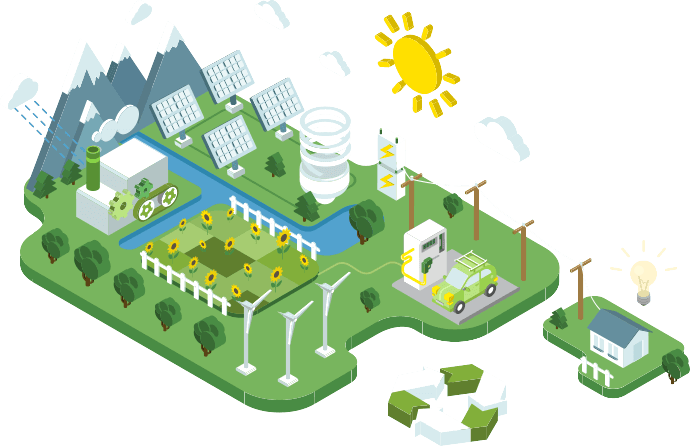
Use of hydrogen across various applications is not new. For over two decades, fuel cell vehicles (FCVs) have travelled on American, Japanese and European roads. Yet the cost of adoption and infrastructure development was a roadblock to widespread usage. Thankfully, companies like Toray are challenging the status quo. Driven by the company’s mantra: “materials change our lives” , Toray is developing a range of groundbreaking materials. From green hydrogen production to transportation, storage and usage, Toray’s efforts are helping the world transition to a society that uses hydrogen gas as its main form of energy.
Advancing fuel cell technology
Toray’s contribution to advancements in FCVs are noteworthy. The company provides electrode base materials for the vehicle fuel cells, plus high-strength carbon fibre and liner resins for high-pressure tanks to hold the hydrogen while on the move. The company’s subsidiary in Germany, Greenerity, is a leading producer of catalyst-coated membranes (CCMs) and membrane electrode assemblies (MEAs), both core components of hydrogen fuel cells.
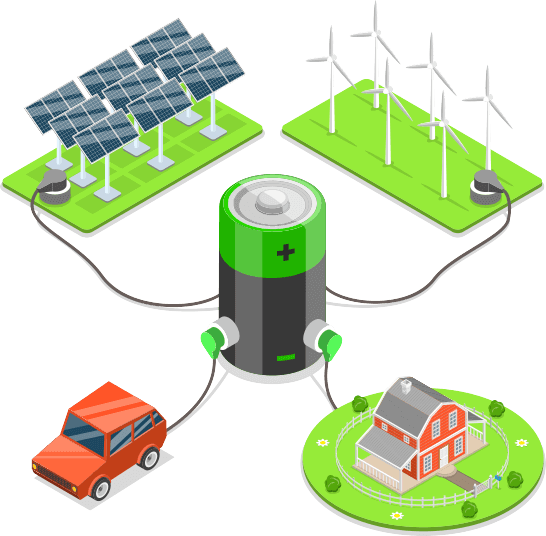
The company’s pioneering electrolyte membrane technology is a potential game changer, with several features making it suitable for hydrogen fuel cells. “Toray’s hydrocarbon-based electrolyte membrane has high proton conductivity, which is about twice that of existing fluoride membranes—especially under high humidity conditions,” explains Mr Yukichi Deguchi, Executive Advisor, Corporate Strategic Planning Division for Toray Industries.
“It has very low gas permeability, which increases the efficiency and safety of hydrogen devices. It also has high mechanical strength, and can withstand high temperatures.” These traits make Toray’s fuel cell membranes more efficient than conventional models. Additionally, the company’s carbon-fibre hydrogen tanks make FCVs lighter and improve their fuel efficiency.
Industrial scalability
Convinced the technology behind its hydrocarbon-based electrolyte membrane could be used in other applications at scale, Toray set about applying it in the production of hydrogen through water electrolysis, and compressing hydrogen for storage and transportation.
Regarding the former, polymer electrolyte membrane (PEM) water electrolysis is rapidly becoming the mainstream solution in this field. This is due to the versatility and high performance of PEMs versus other types of membranes used in water electrolysis. To date, the most common PEMs used in water electrolysis are fluorinated electrolyte membranes. Toray is taking the technology a step further: the company’s hydrocarbon-based electrolyte membrane can be used with twice the current density of fluorinated electrolyte membranes—this produces double the amount of hydrogen generated per membrane area when compared to conventional solutions.
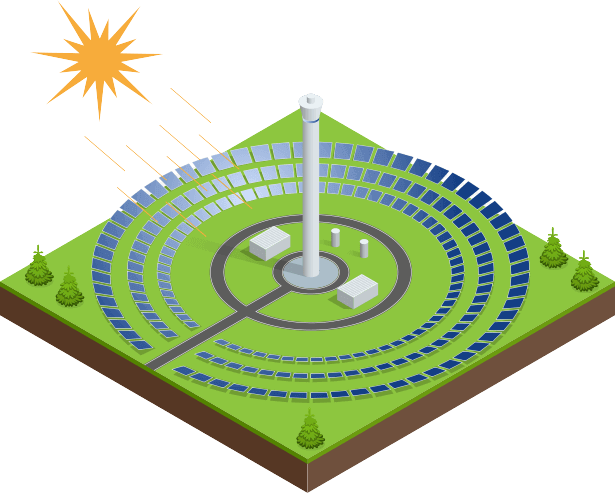
“The characteristics of our technology are expected to help significantly reduce the cost of green hydrogen in the future.”
Mr Yukichi Deguchi,
Executive Advisor, Corporate Strategic Planning Division for Toray Industries
Toray believes that this technology will evolve further, increasing the potential for green hydrogen across a wide range of applications, while reducing manufacturing costs for water electrolysers. “By doubling the current per membrane area we reduce the cost of the equipment required. What’s more, the low membrane resistance and low gas permeation makes the electrolysis system safer, more efficient and thus available to more people and organisations,” enthuses Mr Deguchi. “These characteristics are expected to help significantly reduce the cost of green hydrogen in the future.”
Pilots and prototypes
Both the scaling of water electrolysis in large-scale hydrogen generation, and the provision of heat and transportation fuel on an industrial level, have historically proven challenging. Typically, the production processes are cost-intensive and impractical to deploy.
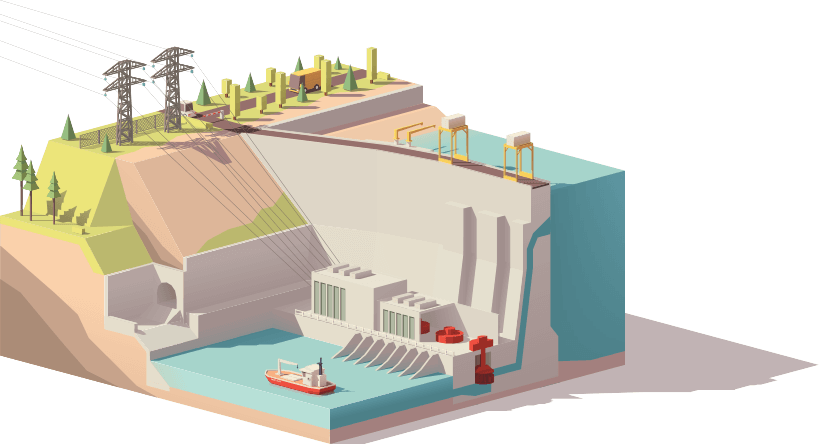
Aspiring to overcome this, Toray partnered with Siemens Energy , combining Toray’s hydrocarbon-based electrolyte membrane and Siemens Energy’s PEM water electrolysis stack system, Elyzer. By making the stack system larger and more modular, and using Toray’s hydrocarbon-based electrolyte membrane, the companies are accelerating the development of industrial-scale low-cost water electrolysis systems.
Further gains are expected from sector coupling—the seamless integration of energy supply and energy end-use across both the power and non-power sectors—to improve the efficiency of energy systems and reduce carbon emissions. Green hydrogen can be used for large-scale power generation, convertible into electricity at the point of demand, as well as being used to provide heat, transportation fuel, or across a variety of industrial applications. A real-world example of this is occurring in Japan’s central Yamanashi Prefecture. Here, Toray is working with a public and private sector partners to develop a large-scale water electrolysis system that leverages hydrocarbon-based electrolyte membranes. The power-to-gas (P2G) system will be installed in large-scale facilities such as factories over the next four years, with the aim of decarbonising heat through the use of hydrogen boilers.
As part of this same P2G project, Toray also collaborated with Kaji Technology to develop Japan’s first demonstration refuelling station for FCVs and other applications using an electrochemical compressor, which pulls low-pressure hydrogen through a PEM and into a high-pressure storage tank. The project, commissioned by Japan’s New Energy and Industrial Technology Development Organisation (NEDO), features Toray’s PEM and stack, and uses oxidation-reduction reactions to compress hydrogen with electricity sourced from renewable energy. The innovative system, which stores hydrogen compressed to 19.6 megapascals, now stands at an electric power storage technology research site in Kofu City, Yamanashi Prefecture.
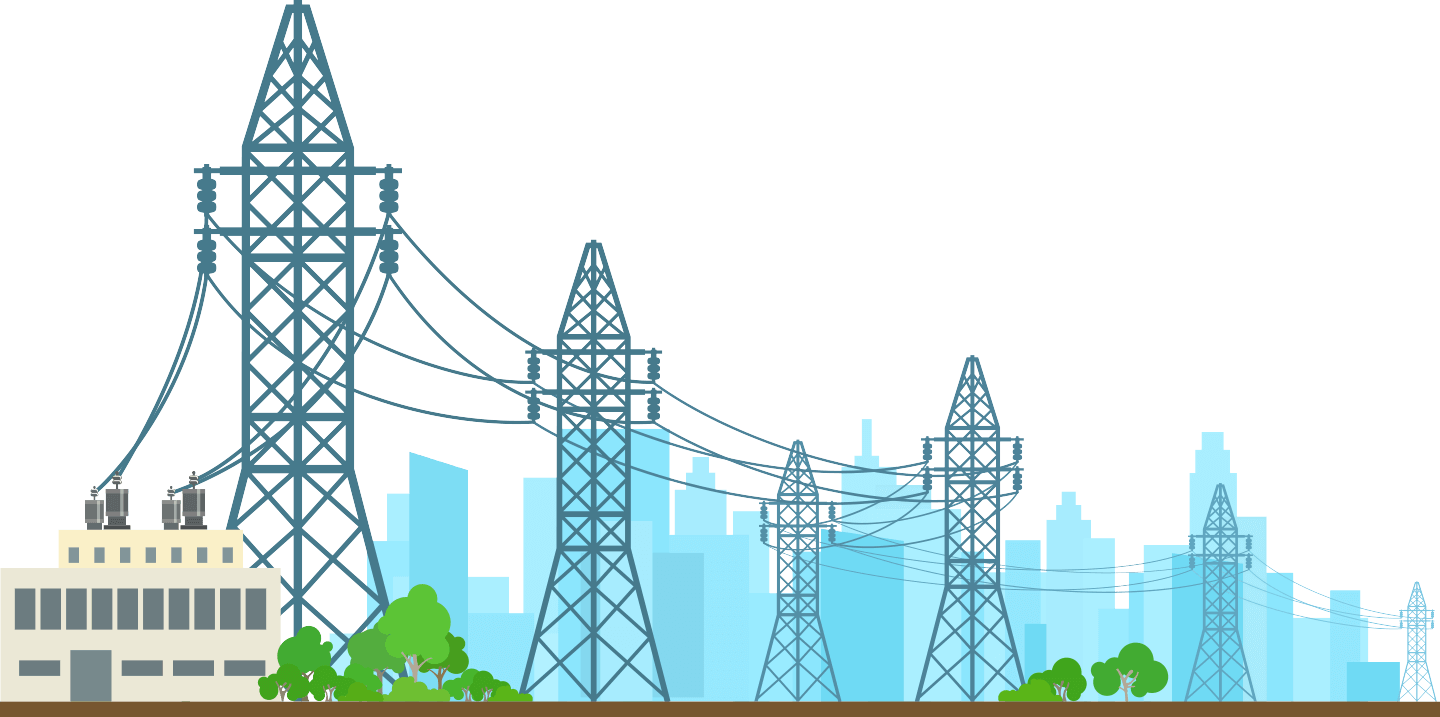
Towards the circular economy
Toray’s leading materials address critical societal needs too. Boeing’s 787 aircraft use the company’s carbon fibre composite materials as primary structural materials, making the aeroplanes lighter and 20% more fuel efficient, allowing for 30% larger windows, and enabling cabins to be quieter with comfortable humidity. Likewise, Toray’s synthetic fibre features in Uniqlo’s HEATTECH, the global retailer’s pioneering winter range of ultra-thin yet extra-warm items.
When assessing the potential of hydrogen to counter climate change and resource depletion, two factors can make the gas viable in the near-term: cost of production, and availability of infrastructure. Toray is leading the charge in both areas. “Toray has always been based on the principle of service to society, and we are convinced that materials have the power to change lives,” enthuses Mr Deguchi. “We recognise that solving global environmental problems, including climate change and ensuring a safe and hygienic living environment, will be the greatest social challenges in the decades to come.”
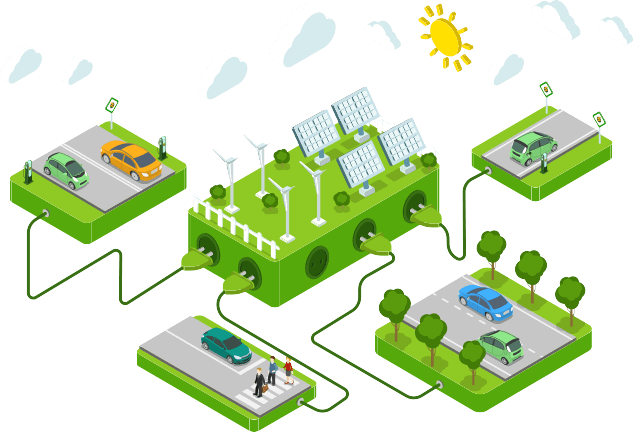
“Hydrogen plays an important role in this kind of carbon recycling.”
Mr Yukichi Deguchi,
Executive Advisor, Corporate Strategic Planning Division for Toray Industries
“Hydrogen plays an important role in this kind of carbon recycling. For example, hydrogen is often used in the reaction between the chemical decomposition and the reuse of useful substances. More directly, it can be combined with the collected CO2 to produce a variety of chemicals, including methane,” explains Mr Deguchi. “The chemical processes and bioprocesses that enable such carbon recycling are an extension of the technologies that chemical companies like Toray have accumulated over the years—and we view them as a great opportunity.”
Toray’s pursuit of the ultimate limits of technology and materials is making the production, transportation, storage and use of green hydrogen rapidly cost-competitive. The company’s breakthroughs are also making a genuinely circular economy possible.
Toray believes the next decade will become green hydrogen’s moment: as it becomes cost-competitive with rival energy sources in terms of production and distribution, and more efficient and environmentally friendly thanks to sector coupling and carbon recycling. All of which underscores the company’s positive contribution to carbon neutrality, solving global environmental problems, and ensuring a safe and hygienic living environment for all.
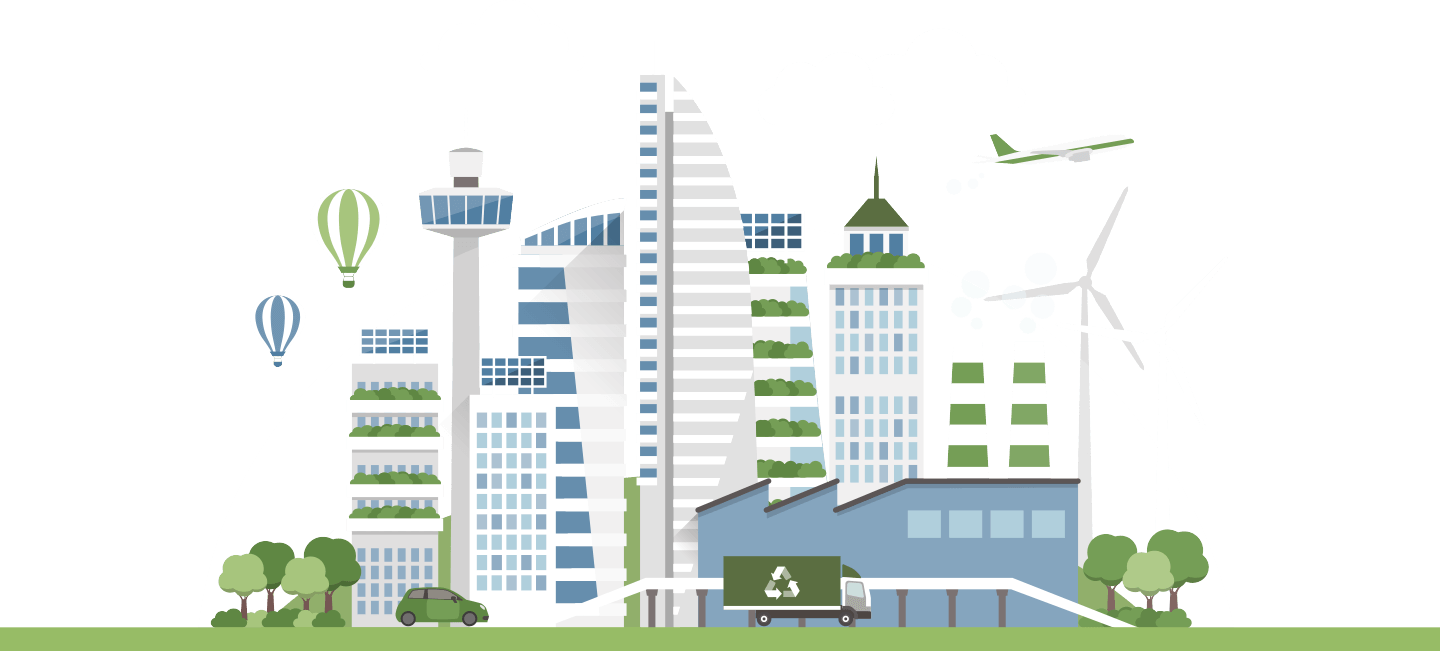